变厚板简介
不等厚轧制板(tailo redrolled blanks,TRB)在国内常被称为变厚板(variable-thickness rolled blanks,VRB)。它是上世纪九十年代初,由德国亚琛工业大学金属研究所最早进行研究,其核心是“柔性轧制技术”,即在钢板轧制过程中通过计算机实时控制轧辊间隙,获取沿轧制方向预先定制的变截面厚度板材。变厚板由于其厚度组合可控制的特点,可以根据汽车结构的承载受力方式以及车身装配条件,灵活选择板料厚度组合,极大地提高了汽车零件的设计空间,通过零件合并等实现了汽车轻量化。
变厚板为车身刚度和强度提供多种柔性的设计方案,目前已成为汽车轻量化的一种重要技术选择方案,在保证车辆安全性的同时实现减重,也受到世界各大汽车制造厂商的青睐。国外关于变厚板的应用技术已经从实验室的研究阶段发展到了工业生产,许多国外高档车型,特别是德系车型,如宝马、奥迪、奔驰、大众和欧宝等,已经开始大量使用变厚板材料。而在国内,对变厚板的研究还处于探索阶段,宝钢研究院已经利用中试轧机成功进行了冷轧变厚板的轧制,宝钢VRB产业大轧机具备批量供货的能力。但是变厚板的厚度变化和变形非均一性形成其独特性,特别是模具设计及制造领域还处于空白阶段。因此对于变厚板冲模坯料定位、厚度过渡区模具零件间隙、模具零件型面加工、回弹处理等关键问题都值得深入研究。
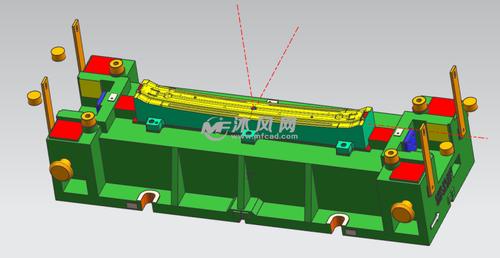
以下对某车型顶盖横梁采用变厚板材料及其工艺性能进行成形工艺仿真分析,完成变厚板模具设计与制造,成功试冲变厚板顶盖横梁零件。
2
变厚板顶盖横梁成形工艺分析
图1 VRB顶盖横梁
顶盖横梁零件是汽车车身在车身骨架中的重要安全承载件,该零件对于提升侧面碰撞安全性及布局结构接头刚度有较大影响,因此其结构特点是在两端与侧围B柱接头位置处应具有较大的厚度以增加刚度。采用VRB顶盖横梁如图1所示,两端厚度1.2mm,中部厚度0.8mm,材料为HC340LA。
图2 VRB顶盖横梁的厚度过渡区的过渡方式
VRB顶盖横梁的厚度过渡采用均匀过渡,两端由1.2mm逐步线性过渡到0.8mm,其厚度过渡区的过渡方式如图2所示。
01
变厚板过渡区模拟
图3 变厚板过渡区离散化示意图
变厚板与一般等厚度钢板的区别在于板料在轧制过程中存在一个连续厚度变化的过渡区,这种厚度上的连续变化也导致了板料在材料性能上的非均一性,从而导致常规用于成形模拟单一材料模型参数不能直接用于变厚板的成形仿真。一方面利用分区离散的方法,将过渡区分区离散为由不同阶梯厚度区的板料(见图3)连接而成,在等厚度区采用同一材料性能,从而可以有效地实现对变厚板过渡区域的材料特性模拟,其中不同厚度离散区域的材料参数通过2个厚度差值得到。
图4 Dynaform软件中实现变厚度板料设置
同时,在Dynaform软件中可以通过关键字控制设置板料的初始厚度,实现坯料由等料厚转变为不等料厚,在Dynaform软件中实现的料厚变化分布如图4所示。
02
成形工艺Autoform粗算分析
目前常用的冲压CAE仿真分析软件有Autoform和Dynaform,两者均可对全工序的冲压过程进行模拟分析。Autoform相对于Dynaform在计算效率上要高很多,并且设置方便简单。分析过程首先用Autoform进行仿真分析,待分析结果稳定后通过CAD建模后,再用Dynaform进行精算,对板料的破裂、起皱、回弹进行分析与预测。
图5 确定冲压方向
通过调整冲压中心坐标并进行冲压方向旋转,确定零件的冲压方向(见图5),保证不能存在负角,脱模角保证3°以上,并且保证拉深的合理性以及后续修边冲孔的便捷性,由图5可知,零件型面整体冲压角度处于安全状态。
图6 仿真分析零件型面设计
零件型面部分设计可分为压料面和工艺补充2个部分。压料面设计通过截面线等手段控制,截面线添加的原则是越少越好,因为截面线越多,压料面的曲率变化越难控制;工艺补充首先需要对主截面形状进行确认,分别是凹、凸模圆角、侧壁倾角以及分型线宽度等,充分保障工艺补充面的整体光顺,如图6所示。
图7 变厚度板料在Autoform中的设置
由于Autoform无法直接设置不等料厚的变化,可利用设置拼焊板的方法,通过添加拼焊线设置不等料厚坯料,如图7所示。
压边力按下式计算:
式中:σ——材料的抗拉强度,MPa;h——板料厚度,mm;L——分模线长度,mm。
由于顶盖横梁成形对于材料流入量要求不大,可选用拉深筋控制压边圈上的材料流入。
图8 顶盖横梁成形FLD图
图9 顶盖横梁成形起皱示意图
通过以上对变厚板板料特性的表征方法及成形工艺进行成形仿真参数设置和分析,仿真分析如图8、图9所示,结果表明该材料特性表征方法用于VRB零件冲压成形数值模拟过程稳定,精度高,结果可靠,该零件采用变厚板方案时的拉深成形性能良好,在拉深件上无开裂现象。零件起皱可以通过起皱准则进行评判,表面起伏高度大于0.03mm时可视为该区域有起皱风险。从仿真分析结果看此件在零件切边区域内的起皱情况符合要求。
03
成形工艺Dynaform精算分析
由于Autoform中构建的型面是较为粗糙的网格数据,无法直接应用于工艺精算和模具结构设计,必须结合Autoform提供的粗算数据构建CAD数模。根据顶盖横梁进行模具设计的相关要求,完成该零件的压料面及工艺补充设计,如图10所示。
图10 顶盖横梁成形型面
在Dynaform中导入上述完成的工艺型面,对其进行网格划分。由于精算对于网格质量要求较高,必须对网格进行质量检查,要求不得出现内部缝隙、局部尖角、重叠网格,并统一法向。
图11变厚度板料在Dynaform中的实现
在Dynaform计算文件中可以对板料初始厚度进行定义,对其进行设置后板料如图11所示,由此可以实现板料薄区和厚区之间的均匀过渡。
根据粗算中确定的边界条件,并结合以上变厚度板料设置方法,对顶盖横梁零件的变厚板方案进行精算分析。在Dynaform分析中通常需要结合FLD图和减薄率对板料是否开裂进行分析,对于单向拉伸区域和双向拉伸区域,减薄超过25%视为破裂;同时在双向拉伸区域,减薄在极限料厚和25%之间,可以通过FLD图进行判断。
图12 顶盖横梁成形后减薄率示意图
变厚度顶盖横梁在成形后的厚度分布情况如图12所示,从图12中可以看到,成形制件在角部上减薄过大,可能会导致现场实际冲压开裂,需要对开裂位置的工艺型面进行修改,直至Dynaform精算中开裂消除。
当零件成形稳定后,将零件回弹计算加入到后期模拟过程中,边界条件采用支撑回弹,得到回弹结果如图13所示。
图13 顶盖横梁精算回弹结果
由图13可以看出,零件回弹量在两端为负值,最大值为1.5mm左右,零件中间基本上没有超差或局部超差不超过0.7mm,根据模拟结果可以判定零件在脱离模具后表现出来的状态是:在冲压方向上,两边向下弯曲,中间向上翘起。
图14 局部回弹补偿方案
为了提前进行回弹处理节省后期调试时间,根据以上模拟结果对零件进行回弹补偿优化。回弹补偿常用的方式有2种:全局补偿和局部补偿。由于不等厚板材的特殊性,且回弹区域较集中在两端,采用局部补偿的方式进行回弹处理,如图14所示。
在冲压方向上,零件两头向下塌,因此需要将两端沿回弹反方向抬起一点,达到补偿效果,同时考虑到不等料厚过渡区域厚度不一致,对过渡区域进行回弹处理可能会导致板料过渡区域与模具零件过渡区域难以吻合,影响模具零件着色效果,因此只选择了端头到接近过渡区域的型面进行回弹补偿,型面最大更改量为2.0mm。
图15 拉深工序模具型面设计
经过以上分析及模具型面设计和改进,得到的顶盖横梁拉深工序模具型面如图15所示。
3
VRB变厚板顶盖横梁模具开发
01
模具型面处理
变厚板模具零件在加工过程中无法沿用传统模具型面加工方法,需要针对变厚板的特点对上、下模型面加工数据进行处理。
图16 变厚板模具型面处理
一般情况下凸、凹模和压边圈的加工数模型面都在同一侧,型面是重合的,加工数据一般通过数控加工程序对上型面进行偏置,得到用来加工凸、凹模和压边圈的下型面。变厚板存在料厚过渡区域,无法用机加工的方法来偏置料厚,因此需要在加工数据中将料厚偏置体现出来,将凸、凹模和压边圈的型面都做出来。在设计工艺阶段型面取零件上表面,那么在加工数据中凸、凹模区域直接使用数模的上、下表面,凹模型面不动,凸模的工艺补充区域和压边圈型面用凹模型面向下偏置料厚,料厚过渡区则通过桥接连接,如图16所示。
02
模具结构设计
变厚板在成形过程中如出现板料位移,容易出现较大的厚度偏差,因此需要对变厚板在整个变形过程中的板料运动状态进行控制。
图17 压边圈侧视图
图18 配重式定位板
由图17可以看出,顶盖横梁的压料面是两头高,中间低,板料刚开始放入的时候,由于重力作用下中间会下垂,板件定位不稳,尤其变厚板特点是中间薄两边厚,中间强度变差,板料中间下垂会导致定位失效,从而导致板料厚度过渡区域与模具厚度过渡区域不一致,影响拉深成形效果。因此,可在压边圈中间采用如图18所示的配重式定位板对板料定位精度进行控制。
图19 顶盖横梁模具下模
考虑到后期方便现场调试,板料厚度过渡区域附近必须要在下模上布置调整垫块,方便调整间隙控制板料流动,如图19所示。
图20 变厚板顶盖横梁
基于以上针对变厚板模具零件加工制造方面的研究,完成了顶盖横梁的零件试制,零件表面光滑平整,无裂纹和皱褶产生,零件尺寸符合要求,如图20所示。
▍原文作者:张文1,2,高永生1,2
▍作者单位:1.宝山钢铁股份有限公司研究院;2.汽车用钢开发与应用技术国家重点实验室(宝钢)