塑件工艺性分析
图1 出风口塑件外形结构
图2 出风口塑件局部结构
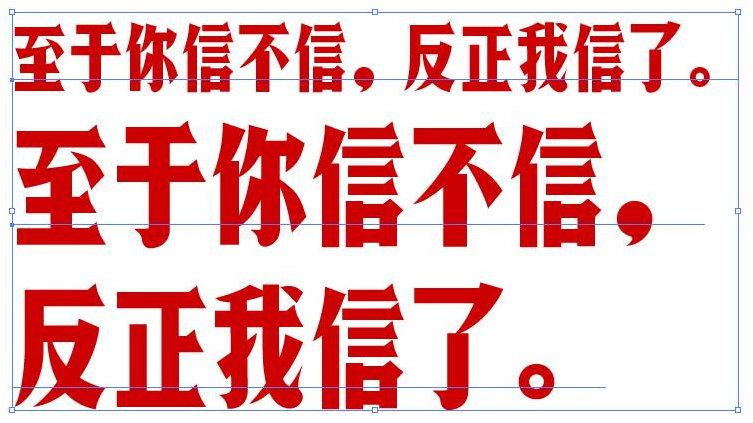
汽车空调出风口塑件材料为结晶型工程塑料PBT+PCGF10,外形尺寸为232mm×84mm×37mm,平均壁厚2.0mm,内部存在众多的加强筋和倒扣,单件质量为80g,塑件外形结构如图1所示,局部结构如图2所示。塑件外表面为汽车内饰的直接外观面,不允许存在熔接痕、气穴等缺陷,因此塑件的分型面位置、台阶、纹路质量以及熔接痕位置和深度是模具设计的重点和难点;塑件内部筋位、倒扣较多,壁厚不均匀,容易出现短射、充填不满等注射缺陷。为避免塑件左、右出风口产生色差以及提高生产效率,模具采用1模2腔结构形式,同时成型左、右出风口塑件。
基于Moldex3D分析的浇注系统设计
根据塑件的结构特点以及全自动化生产要求,注射成型的浇注系统采用单点开放式热流道+单点潜伏式浇口的进料方式。经计算采用Synven⁃tive(圣万提)型号为GAKNM170VCV1ETypeManifoldABL的热流道。
塑件中间存在孔洞,在外观面上容易产生熔接痕,为减少熔接痕,可利用CAE分析并设计合适的浇口位置。熔接痕产生于2股低温熔体的相遇位置,结合塑件的结构特点,初步选择2种浇口位置进行分析。方案一:采用潜伏式浇口,浇口设计在塑件中间没有滑块的区域,浇注系统的位置、流道及浇口大小如图3(a)所示。方案二:同样采用潜伏式浇口,浇口设计在塑件边角没有滑块的区域,浇注系统的位置、流道和浇口大小如图3(b)所示。
(a)方案一
(b)方案二
图3 2种进浇方案
方案一的熔接痕的分析结果如图4所示,熔接痕出现在出风口叶片的中间位置,容易发生困气和断裂,最大变形量达到了1.066mm,翘曲变形出现在塑件的一角,影响出风口和其他零部件的装配。方案二的熔接痕分析结果如图6所示,熔接痕仍然出现在出风口叶片的中间位置,改善效果有限,最大变形量为0.425mm,与方案一相比翘曲变形明显减小。最终选择方案二的浇注方式。
图4 方案一熔接痕分析
图6 方案二熔接痕分布
图8 塑件壁厚调整方案
根据经验,可以通过调整出风口叶片的壁厚改善外观面熔接痕的位置,塑件壁厚调整方案如图8所示。采用方案二的浇注方式,模流分析计算后结果如图9所示,熔接痕由叶片中间位置移动到叶片边上,并且调整壁厚后的翘曲变形为0.425mm,最终塑件翘曲变形和熔接痕都得到改善,熔接痕位置不影响塑件的使用性能,修改壁厚调整方案可行。
图9 调整壁厚后熔接痕位置
模具关键结构设计
01滑块结构设计由图1可知,塑件四周有多个孔位,需要设计滑块抽芯机构。行程不大的采用机械式斜导柱抽芯;行程大的位置采用液压缸抽芯机构,且大部分布置在动模一侧,动模滑块结构如图10(a)所示。出风口处的叶片结构也需要一个带角度的滑块抽芯机构脱模,如图10(b)所示。
(a)动模滑块
(b)定模滑块
图10 滑块结构
PBT+PC GF10的流动性好,塑件容易在滑块等活动处产生飞边,因此在滑块配合处做一定斜度避免飞边的产生;为了防止困气造成塑件内表面的筋条填充不满,将动模型芯设计成镶拼结构,利用镶件间隙排气。
02排气系统设计塑件筋条多、壁厚薄,最薄筋条处为0.5 mm,如果排气不良容易造成筋条填充不满等缺陷,故排气系统的设计极为关键。现主要利用镶拼结构实现排气,筋条主要在动模成型,故动模采用不同的小镶件组合的镶拼结构。定模形状比较简单,不需要做成镶拼结构,只需要在定模滑块和主镶件附近的分型外圈上开设一圈排气槽,实现排气。
03冷却系统设计冷却水路的设计应尽量保证模具冷却均匀、迅速,缩短成型周期,模具入水口和出水口的温差应<2°C。最后结合模具结构的镶拼结构和推杆的排布,动模、定模冷却水路分布如图12所示。
(a)动模冷却水路
(b)定模冷却水路
图12 冷却水路分布
试模验证及批量化生产
通过CAE模拟分析及结合实际生产经验开发的汽车空调出风口模具实物如图13所示,生产实践证明设计的浇注系统、镶拼镶件、抽芯机构、冷却系统、排气系统等模具关键部位的设计合理可行。
(a)装配后的动模
(b)装配后的定模
图13 出风口模具
经检验,多批次的塑件无注射缺陷,合格率达100%,塑件的尺寸经过游标卡尺和光学投影仪等设备检测都符合2D图纸尺寸公差要求,满足客户的需求。
欢迎大家关注 !
!
!
每天定时更新模具设计学习视频!
!
!
!
!
!
!
!
!
!
!
!
!
!