随着CAE分析技术的日臻成熟,对复杂冲压过程的仿真日益完善,可以通过前期模拟分析制件成形过程中存在的各种缺陷,通过前期提出制件结构设计变更及调整冲压工艺,避免后期实际模具开发时产生的整改成本或制件出现无法更改的质量缺陷。
车身产品设计工程师在设计过程中主要关注满足车身性能及各种配接要求,对制造可行性关注度不高,经常出现某些制件制造难度相对较高,甚至无法制造,所以同步工程分析在新车型开发过程中起着至关重要的作用。在某新车型开展同步工程分析过程中,发现后轮罩外板设计存在很大的制造风险,如图1所示。
使用AutoForm软件对其进行模拟分析,发现以下几处主要风险点:
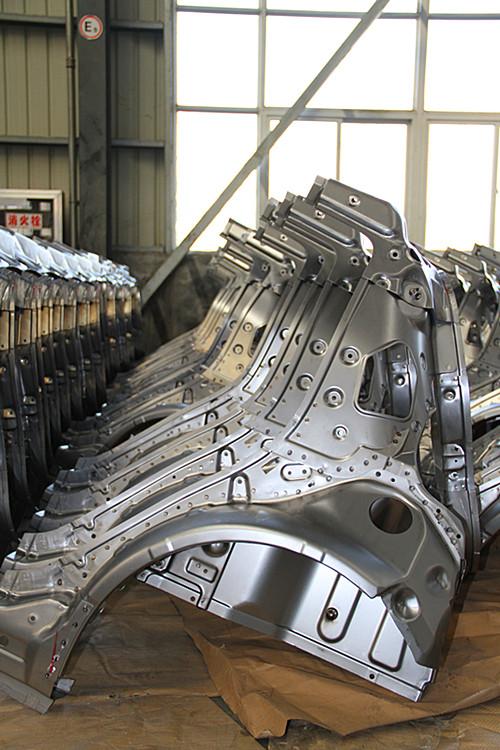
01
Ⅰ、Ⅱ处存在立壁加强筋,顶部圆角出现多处台阶且不光顺,拉深过程中易出现应力集中,产生开裂。
02
Ⅲ处落差大(32mm),且立壁拔模角小。
03
Ⅳ处立壁拔模角小,两处立壁平面夹角为锐角,该结构易出现顶部开裂,角部起皱现象。
经过CAE分析,开裂、起皱情况如图2和图3所示。
图2 初始制件开裂情况
图3 初始制件角部起皱情况
由CAE分析结果可知,初始制件顶部所有存在台阶的圆角均产生开裂,型面变化剧烈位置(Ⅳ处)开裂严重,Ⅲ处角部起皱严重。
针对分析结果提出更改建议:
01
Ⅰ、Ⅱ处立壁加强筋在到达顶部圆角之前消失,以保证顶部圆角的光顺性,并在顶部非搭接区域增加斜面,使拉深过程中顶部接触由点接触变为线接触。
02
Ⅲ处在后部增加一个斜面削掉易开裂尖点,前部立壁采用整形工艺成形。
03
Ⅳ处在不搭接区域增加斜面削隙开裂尖点,底部增加吸皱三角筋,增加的吸皱筋不能破坏底部法兰圆角边界。
变更后的制件结构如图4所示,更改后CAE分析结果如图5、图6所示。
(a)主视图
(b)轴侧图
图4 更改后的制件结构
图5 更改后CAE减薄情况
图6 更改后角部起皱分析情况
由图5可知,更改后制件有2处尖点位置减薄超过20%,最大减薄率为21.1%,由于轮罩外板材质为DC06,最大减薄率未超过极限减薄率23%,且最大减薄位置在尖点区域,所以更改后制件满足成形要求。