2 顶盖缺陷
图3所示为顶盖实物缺陷,尾部侧整形后产生 缺陷为 R 角不顺(见图 3(a))及表面凹陷(见图 3 (b)),缺陷等级高,R角不顺导致装车后此处与扰流 板间隙不均(见图3 (c)),连同表 面凹陷 影响整车外 观品质。
3 缺陷产生原因分析
图4所示为尾部侧整形的CAE模拟结果,从图 4中各位置的剖面R角放大可以看出,恒定负角位A-A剖面及正角位C-C剖面的R角与凸模符形,只有过渡区域B-B剖面的R角是变形的,最终导致此区域的R角不顺以及表面凹陷,查看板件与下模接触距离的CAE分析结果,发现过渡区域板件R角与下模的接触距离最大,如图5所示。产生缺陷的主要原因:侧整形时刀块接触板件的时间不一致,恒定负角位最先接触,然后往正角位挤料,过渡区域是接触料变化的区域,也是缺陷容易产生的位置。零件两侧整形量较大,侧整过渡区域较急剧,过渡处成形应力变化导致R角变形,产生表面缺陷。过渡区域的造型和缺陷有较大关系,其他条件一致的情况下,不同的过渡区域造型会产生不同结果。
4 缺陷解决措施
方案1:在确认缺陷处模具基准、研合及尾部压 料板压力合格的基础上,通过控制侧整形时尾部的 材料流入量以改善缺陷。图6所示为通过增加阻料 筋控制侧整形时尾部材料流入量,CAE分析结果如 图7所示,板件与下模接触距离相对未增加阻料筋 前(见图5)明显减小,即R角变形缺陷有所改善,但 是尾部棱线处的减薄率增大,存在开裂风险(见图 8)。后期经过现场尾部贴纱布试验,结果与CAE相 符,顶盖尾部的流入量减少,缺陷相应减少,但是减 少到一定量后尾部开裂,而缺陷还未完全消除,如 图9所示。
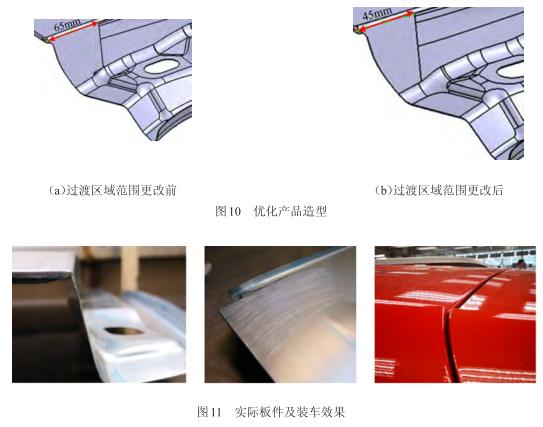
通过控制材料流入量优化该缺陷具有直接的 效果,但零件侧整形量较大,优化过程会产生开裂, 在产品造型允许的前提下(即开裂安全欲度大),该 方案整改是最有效的。按此方案钳工现场优化阻 料筋至零件不开裂,R角变形缺陷有所减缓,但未完 全消除,在此基础上再进行方案2优化。方案2:优化产品造型,把原过渡区域加大后通 过CAE模拟,从板件与下模接触距离的分析结果 看,R角变形缺陷也有明显改善的趋势。在咨询产 品过渡区加长的可行性后,最终过渡区域在原有基 础上加长了15 mm,即正角位区域范围由原来的60 mm缩短至45 mm(见图10)。模具按此新造型更改 加工完现场压件后,顶盖R角不顺及A面变形缺陷 已经消除(见图11),由此可以得出,更改产品造型 是一种较好解决板件缺陷的方法。
▍原文作者:黄渊燊1,王双明 1,王小凯 2
▍作者单位:1.柳州福臻车体实业有限公司;2.神龙汽车有限公司