实际上钣金裂纹的起点区域大部分都是在焊点区域,对于焊点区域的疲劳模拟是CAE技术的关键。
随着汽车行业的飞速发展,汽车的需求量及出口量不断增加,对于汽车驾驶性能、安全性能的要求也在逐步的完善和提高。汽车企业在针对当前车型进行开发时,不仅需要满足不同的法规评价,还存在一系列的内部实验标准,用于不断改善车辆的质量和乘用体验。
目前,在车辆疲劳工况中,现有的仿真技术无法准确的模拟及预测钣金连接区域的疲劳开裂问题,仍然需要进行多轮疲劳物理试验。试验的周期单轮需要一个月左右,经过上万次的外力加载,试验不仅周期长,而且耗费企业巨大的开发费用成本。在车辆疲劳现有仿真技术中,车辆钣金件在模型建立时简化为壳单元,连接处使用刚性连接建立,因此无法准确模拟钣金连接区域的受力状况,如果对整个车辆及所有钣金连接处使用超细化模型,整车模型有限元网格数目因此会增加500~1000倍,虽然能准确的模拟钣金及其连接处的受力及失效情况,但是由于整车模型巨大,会导致计算效率极其低下的问题。
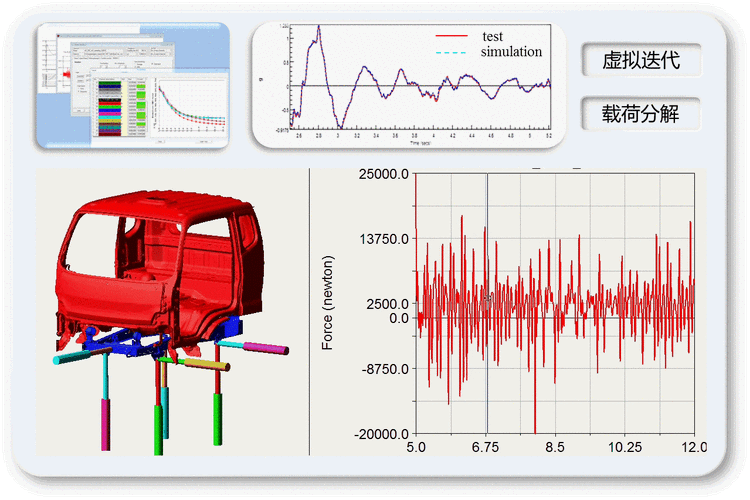
(图片来自网络侵删)
因此,如何通过疲劳仿真分析模拟来高效并准确模拟钣金件连接处受力情况及疲劳开裂的风险,减少所需进行的整车实验的次数,提高整车开发流程的效率仍然是一个具有挑战性的课题